FMEA Without Tears
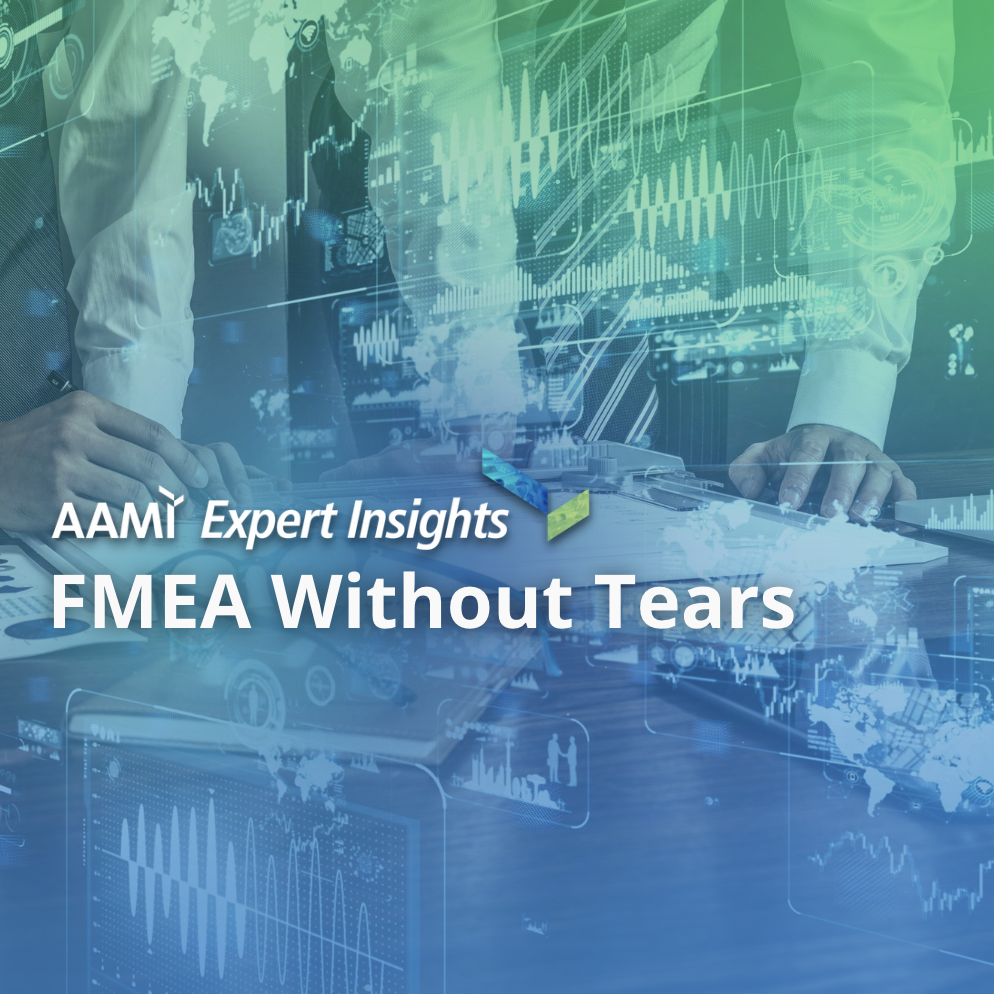
Upcoming Virtual Courses
Overview
Philip Crosley recognized similar issues with quality in general when he wrote a seminal book titled, “Quality Without Tears.” Since then, many good people have successfully facilitated the integration of quality systems into organizations. Likewise, the goal of this webinar is to facilitate the successful application of FMEA as a valuable risk analysis and risk management tool.
This webinar will give you an opportunity to hear directly from an industry expert who has facilitated the application of FMEA across a wide variety of organizations. He successfully leads teams tasked with risk analysis and risk management through a mentoring and “divide-and-conquer” approach. In most cases, an FMEA exercise lasts 1-4 hours, depending on the complexity and risk involved. In one case, a thorough FMEA for a complex, Class 3 medical device was completed, documented, and submitted in only three days. In another case, a risk analysis was conducted in 30 minutes using a simplified FMEA! But the key measure of success is that all team members feel that their effort yielded credible and actionable results.
Objectives
Over the course of two hours, the program will:
- Introduce the key concepts of Hazard and Risk Analysis
- Illustrate how a simplified FMEA can yield results in a flash
- Define the industry-standard format for an FMEA
- Provide examples of how to facilitate an FMEA team effort
- Discuss ways to avoid the common misuses and abuses of FMEAs
Who Should Attend?
This material will appeal to quality professionals, managers, and FDA staff. Instruction is targeted to professionals involved in risk analysis and management. Given the broad application of risk analysis, this material will be of value to professionals working across the entire product lifecycle, including R&D, manufacturing, packaging, logistics, supplier quality, marketing, sales, product support, and regulatory affairs. It will also appeal to FDA staff interested in the application of best practices to support quality systems.