Design Control Requirements - Integrating the Quality System Regulation
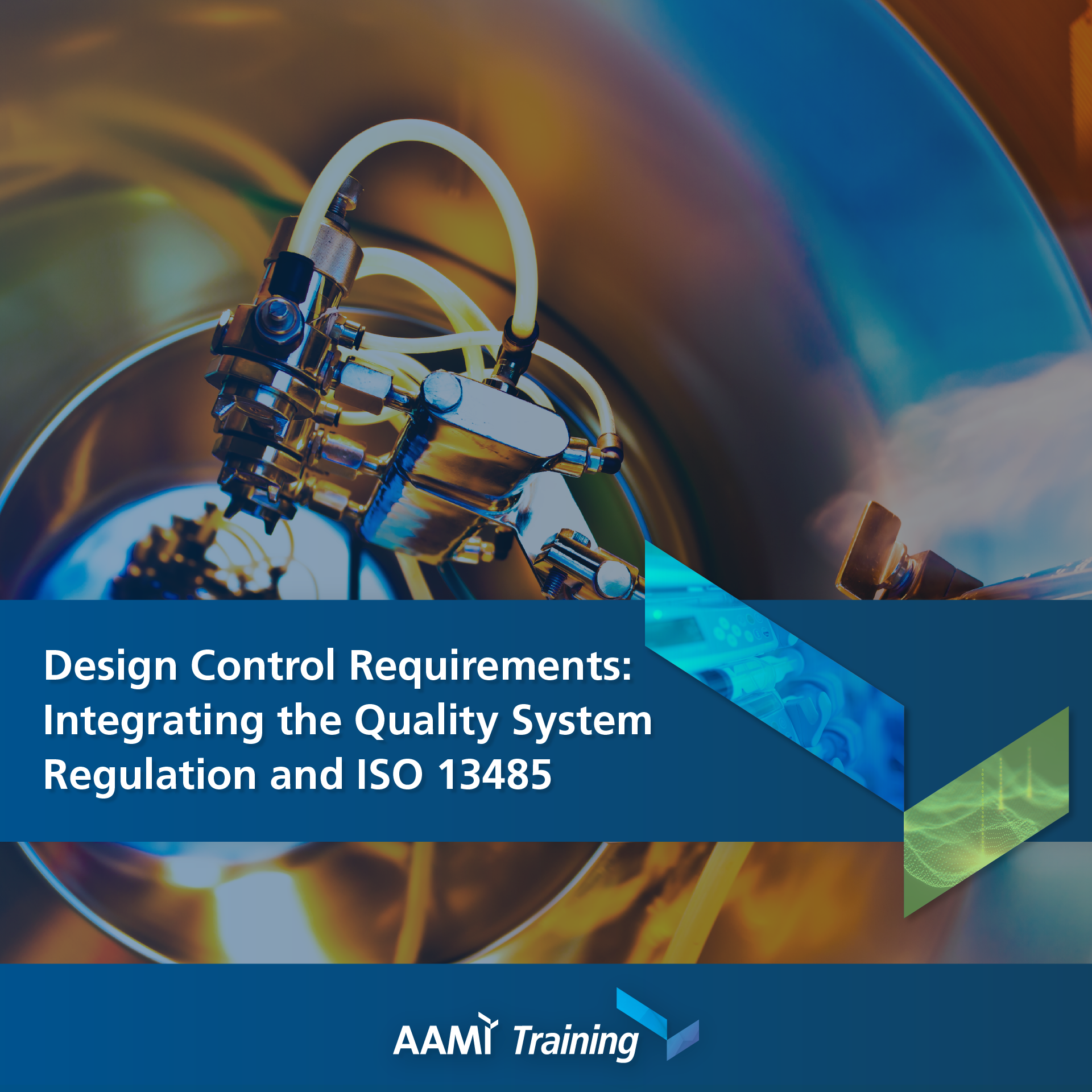
Upcoming Virtual Courses
Quality Systems
Design Control Requirements - Integrating the Quality System Regulation (Sept25)
Sep 9 to Sep 11, 2025
Quality Systems
Design Control Requirements - Integrating the QMSR (Dublin IRE | Oct 2025)
Oct 7 to Oct 9, 2025
Quality Systems
Design Control Requirements - Integrating the Quality System Regulation (Dec25)
Dec 2 to Dec 4, 2025
Overview
This intensive 3 – day course provides complete coverage of design control requirements for FDA Quality System Regulation, ANSI/AAMI/ISO 13485:2016, and the Medical Device Single Audit Program (MDSAP). With the participation of FDA representatives
during the entire course, attendees have the unique opportunity to participate in a shared learning experience.
Objectives
Upon completing this course, participants will be equipped with the information to able to evaluate the degree of compliance of a design control system, including identification of noncompliance issues, and be prepared to implement the improvements needed
to meet requirements.
This highly interactive course engages the learner with in-depth discussion of industry best practices to learn how industry leaders address design control challenges. Exercises are designed to build a solid understanding for developing and applying design
control requirements. Attendees will participate in structured discussions with their peers to develop solutions to solve current issues.
Examples of design control tools, templates, and practices, in use by medical device companies, stimulate discussion and provide a practical resource for future reference. Case studies and situation analyses are used throughout the program to help participants
analyze potential areas of noncompliance, identify improvements, and evaluate the various methods of managing a design control program.
Course content is the culmination of years of consensus development on the part of a respected group of quality system experts from leading device manufacturing companies, FDA, and industry consultants.
Who Should Attend?
Instruction is targeted to professionals involved in meeting design control requirements such as those in regulatory affairs, quality assurance, design engineering, manufacturing, operations, and members of research and development or new product development
teams.
Materials
Fee includes a printed copy of the textbook, The Quality System Compendium, and electronic versions of the PowerPoint presentations and case studies, pertinent FDA documents, additional references, and access to the online exam.
Virtual Training Information
Our virtual training environment allows you to have direct interaction with your instructors and your fellow attendees. AAMI uses Zoom for virtual classes. You can test your connectivity and ability to use Zoom at zoom.us/test.
For virtual training courses, we request that you register at least one week in advance of the course start date to allow sufficient time for shipping of training materials and devices (Please allow two weeks for non-U.S. addresses). If you register within these time frames, AAMI cannot guarantee you will receive material prior to the start of the course but you will have access to digital versions of the materials. If you have any questions, please email education@aami.org.